Application of open steel barrel barrel round curling
Application of open steel barrel barrel round curling
Li Guixiang, Jinshui County Metal Packaging Container Factory, Yunnan Province
Various types of steel drums have different structures for crimping. In order to improve the quality of the edge of the open steel barrel, it is necessary to discuss and study the crimping principle in order to better solve the existing problems of the crimping.
First, the concept, mechanism and forming of the curling
In order to increase the rigidity and strength of a part or finished product, the process of curling its edges into different shapes is called crimping. There are many parts or finished products that need to be crimped, such as various fairings, hoods, pots, pots, cans, boxes, buckets, lids, cans, and oysters. Curling can be divided into two categories: manual crimping and mechanical crimping. The manual crimping can be divided into two types: a wire crimping and a hollow crimping. . The mechanical crimping is made of mechanical equipment, mold and forming wheel set. Among them, it can be divided into two types: stamping and bending curling and roller spinning and crimping, such as the locking of the spiral ring and the opening of the open steel drum to the mechanical crimping. Mechanical crimping is commonly used in steel drum production. Because the design principle of the main working curve of the punched and curved crimping groove and the spinning and rolling groove is similar, this paper only discusses the mechanism of the spinning and crimping.
What is mechanical spinning curling? Any method of making a relative rotation between the roller and the workpiece by mechanical means, while applying a radial or axial feed force to the workpiece, and causing the edge of the workpiece to be curled is called a spinning bead. Conventionally, the method of re-compression or compaction of the portion after crimping is called crimping.
The mechanism of curl formation is that under the action of rolling pressure, the workpiece is partially deformed by plastic deformation, and a new balance is reached. The curling method obtains a rounded or rounded edge, which is mostly used for stamping and manual crimping. Winding crimping applications are more common in spinning beading. The stamping crimping groove can be designed according to the winding crimping principle. The effect is much better than the design of the curved beading principle.
The method and process of generally winding the edge of the wound portion in a loop shape is called a spinning bead. The rule that the difference between the diameters of the two sections being equal to the diameter of the coil is equal to the thickness of the coil equal to one-half of the thickness of the coil is simply referred to as the winding principle. We also refer to the curve composed of two arcs as the winding curve. As shown in Figure 1.
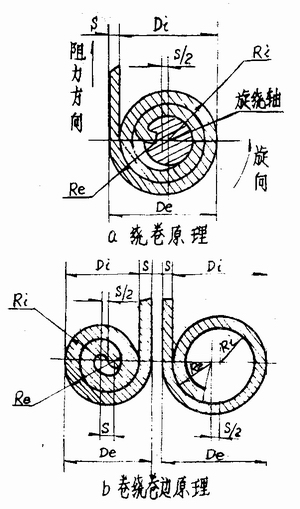

Figure 1 crimping schematic
If you want to wind the edge of a workpiece into a winding curve, you must use multiple crimping methods, and the curve and groove width used for each curl are different. It can be seen from Fig. 2 that the curvature of the inner bead is large and the curvature of the outer bead is small. The law of the radius of curvature of the bead is gradually increased from the inside to the outside, and is more than one roll per roll. The radius of curvature is increased by a thick material.
Figure 2 Round crimping forming process
It can be seen that the processing step of the roll forming is to first roll the inner layer with a small radius of curl, and then use the roller with a small level of curvature to process the middle layer having a larger radius of curvature. This gradually achieves the purpose of curling from the inside to the outside, and finally the outermost shape of the curl. In order to make the shape of the curl ideal, the opening of the roller should be as fine as possible, that is, the more the number of intermediate processing, the more the number of rolling, the better the formed curl forming. . In fact, the design and production of the workpiece is almost no more than three times to meet the requirements.
Second, the application of full-open steel barrel barrel round curling
Figure 3 Unmodified front barrel curling diagram
In our factory, the full-opening steel barrel barrel was crimped before the required roller and tire mold were designed according to Figure 3, and the unfolding length was calculated. This single-arc crimping (also known as coiling) has the following problems:
1. The coiled tube opening cannot be closed, and if it is close, it needs to be pressed a second time.
2. It can only be made if the radius of the coil is less than 3.3 times and the thickness of the coil is thick. If the radius is too large, it will wrinkle due to instability, affecting the quality of the coil, and even impossible to make.
3. The coil has low strength. If a wire coiled tube is used, it will partially wrinkle at the outer edge.
4. Production efficiency is low. During the forming process of the coiled tubing, the rotational speed of the wound workpiece and the axial feed speed of the roller are limited, and it cannot be fed quickly, otherwise large wave wrinkles, cracks, etc. will occur, and even waste products may be caused.
For the above reasons, the curling produced does not meet the design requirements. Generally obtained are coiled tubes that are oblate or that are difficult to close together.
It is a big step forward to apply the winding mechanical crimping bead to the open steel barrel mouth. The barrel-rolling tube structure can be in a variety of different forms (as shown in Figure 4), and the coiling process can be completed once in the axial direction. Flexible and external volumes are available as needed. The method of feeding the roller along the busbar can be used to make the barrel edge of the cone barrel, which has been successful. If it is necessary to increase the strength of the barrel mouth, 2-3 steps can be used, that is, the conventional method of first turning and then crimping is adopted. If the crimping roller is designed according to the principle of mechanical spinning and crimping, a wound-type solid coiled tube can be obtained. Thereby, the strength and quality of the bead curling are greatly improved.
Figure 4 Various forms of barrel coil
Generally, the opening of the barrel of the open steel barrel is preferably carried out by axially feeding the roller once. This can greatly improve work efficiency and product quality, making it look good. The structure and working example of the crimping roller are shown in Figure 5. The processing of the barrel edge curling of our factory was carried out on the old CA6150 lathe. The roller is axially fed once to complete the barrel curling.
The utility model has the advantages that the economical and practical multi-mode wheel set is simple in design, has the versatility, and can solve the hemming processing problem without re-making special equipment, and the multi-hem quality is stable, and the continuous operation is carried out without stopping the main machine, and the efficiency is high. wide range. When processing steel drums with different diameters and heights: only need to change the front and rear placenta can be designed into the same wheel set and other movable couplings for two more work, each shift can produce diameter 276-400mm, height 320-700mm, material 960 steel drums with a thickness of 0.35-0.8 mm (1300 in the factory working day) are easy to operate, safe and reliable.
1-triangle collet; 2-clamping mandrel; 3-front tire mold assembly; 4-steel barrel workpiece; 5-post tire mold; 6-tool holder; 7-roller assembly; 8-tail assembly; 9-active shaft assembly
Figure 5 Rolling die wheel structure and working examples
Another feature of this hemming method is that the workpiece floats as it rotates. When the radius of the coiled tube is greater than 3.3 times and the thickness of the coil is thicker, the method of increasing the amount of floating is used for crimping, and the effect is better. The so-called floating beading means that the diameter of the rear tire mold is different from the inner diameter of the steel drum being wound. The method of floating rotation of the steel drum and the calculation method of the floating amount during the crimping process will be described in detail in the next issue. It should be noted that when there is no floating amount, the curling effect is poor, and the curling effect is better.
The Shuttle Bus our factory producing include 8,11,14 and 23 seaters,can be with gas or battery power, it is mainly used for passengers transportation,sightseeing,touring,,etc, it come with the luxury seats,fantastic electronic systems,like mega phones,music palyer,radios that enable the tourists a enjoyable touring experience,in the mean time, its max speed is not high,just up to 35km/h,this is a very important for its safty, normally we enquip our shuttle buses with the 7.5kw powerful motor and the 210ah 72v battery to make sure its high performance.
Gas Shuttle Bus,Electric Shuttle Bus,14 Seat Electric Shuttle Bus,23 Seat Electric Shuttle Bus,Shuttle Bus
Yongkang Jinghang Sightseeing Vehicle Co., Ltd. , http://www.jhgolfcarts.com